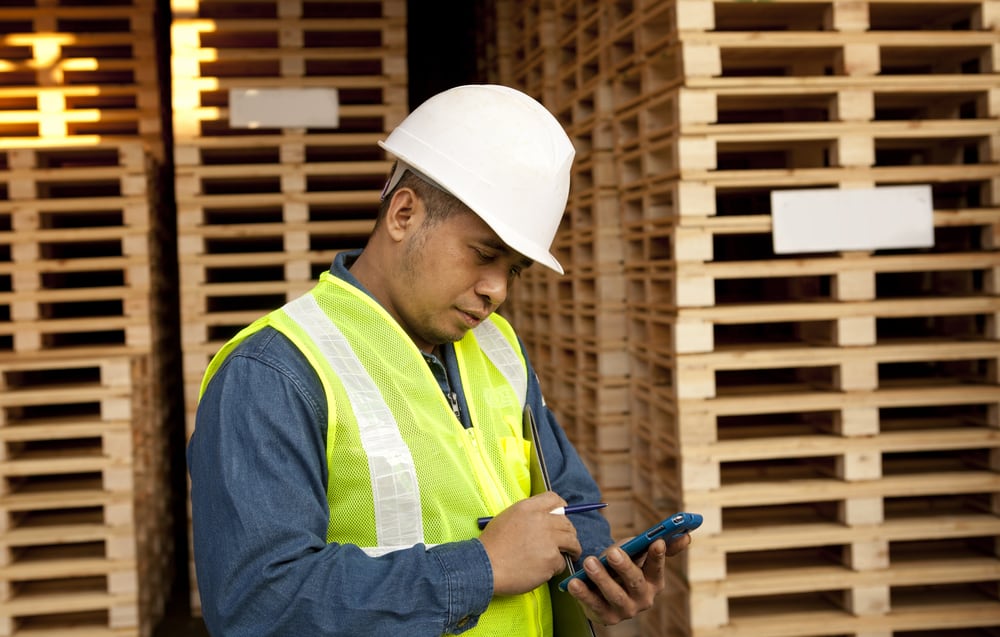
What are the dangers?
Wood dust can enter the body through the nose, mouth or even the eyes. Larger particles may well be coughed, sneezed or spat out, but smaller particles may be inhaled further into the lungs, where they can cause serious long-term health problems, such as
- lung cancer
- nasal cancer from hardwood dusts
- asthma
- chronic obstructive pulmonary disease (COPD)
Wood dust can also contain bacteria and fungal and moss spores present from when the timber was felled and cut. These can also cause respiratory diseases.
According to the HSE, occupational lung disease causes the death of 12,000 people annually, and there are an estimated 19,000 new cases of breathing and lung problems each year. Not all of these are in the timber industry, but it will come as no surprise to learn that carpenters and joiners are four times more likely to develop asthma than workers in other sectors.
Fire and Explosion
Flash fires can happen if part of an unconfined cloud of wood dust ignites and the flames rapidly spread through the rest of the cloud. Alternatively, if the wood dust is contained and pressure builds up, an explosion can occur if an ignition source is present. Different factors will affect how severe the explosion can be, including:
- The type and concentration of wood dust
- Particle size distribution
- Moisture content
- Size of the source of ignition
- Strength of the enclosure
Case study
A furniture company was fined £16,000 after it repeatedly failed to protect its employees from exposure to wood dust.
The company was inspected by the HSE on two separate occasions over a two-year period – with both identifying identical breaches.
A visit in December 2019 found significant breaches of the Control of Substances Hazardous to Health Regulations 2002 (also known as COSHH). This led to six improvement notices being served. These included requirements for the company to carry out examinations of its wood dust extraction systems and to test for face fitting where employees were required to wear face masks.
However, another visit to the same premises in November 2021 found identical breaches and again improvement notices were served.
The inspection was part of a national campaign targeting woodworking businesses. On this occasion, the failure to ensure control of exposure to wood dust resulted in the HSE prosecuting the company, which pleaded guilty to breaching Regulations 7(1) and 9(2)(a). They were fined £16,000 and ordered to pay £3,008 costs.
The problem still remains a real one in the woodworking industry.
In 2022/23, HSE carried out more than 1,000 woodworking inspections and found 78% of businesses were not compliant in protecting workers from respiratory sensitisers (primarily hardwood, softwood and composite material dust). This resulted in 402 enforcement actions taken by HSE.
In January 2024, a manufacturing company was fined £15,000 after exposing its own workers to wood dust and failing to comply with two improvement notices.
What the law says
Regulation 7 of COSHH sets out the legal requirements to protect workers from risks relating to hazardous substances at work.
Under COSHH, employers (including contractors) have a duty to carry out a suitable and sufficient risk assessment and take steps to ensure exposure is either prevented or adequately controlled.
Those steps include:
- Devising and implementing safe systems of work
- Drafting and following a health and safety policy
- Providing employees with appropriate personal protective equipment if this is identified as a need under the risk assessment. In the case of wood dust, this will be respiratory protective equipment (RPE)
- Carrying out health surveillance (see below)
- Removing dust before it builds up and presents the risk of a fire or explosion
- Installing local exhaust ventilation (LEV) where necessary, and arranging for its maintenance by a competent person. This is a very technical area and the advice and guidance of experts and the manufacturer should be followed
- Devise and implement training for employees in how to work safely and what precautions to take. Again, this is a highly specialised area of training, and employers should be honest about their ability and competence to deliver it. An external training provider, preferably a health and safety expert should be used to ensure the training is both suitable and sufficient for the workplace and the risks involved.
Health surveillance
Given what has already been said about the health risks of inhaling wood dust, employers need to have as much information as possible, as soon as possible, about any health problems in the workforce. This can most effectively be done through a suitable and sufficient health surveillance programme.
As with all health and safety matters, a health surveillance programme should be administered either by, or with the advice of, an occupational health professional (doctor or nurse) with the relevant skills, competence and experience for health risks in woodworking.
The health surveillance programme should cover all workers who might breathe in or be exposed to wood dust.
Respiratory protective equipment
If a risk assessment identifies that RPE is needed, then workers at risk should receive training so that they understand:
- the reason for it being worn;
- how to use it correctly;
- what to check before using it;
- how to clean, maintain and store it
- when to discard it if it’s disposable;
- the system by which faults in the RPE can be reported
RPE is considered to be the least effective control measure as it only protects the individual wearing it (unlike LEV which will help prevent everyone in the workplace) and is dependent on it being used correctly.